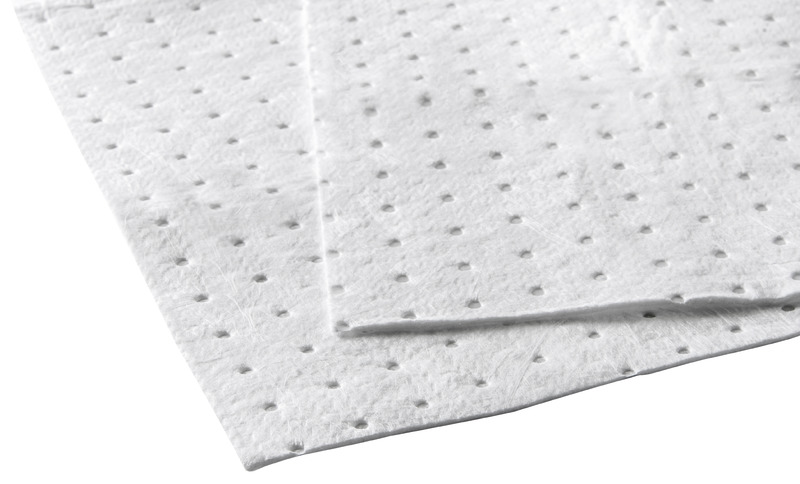
Oil spills can cause serious damage to the environment and industries. That’s why oil absorbent materials play a crucial role in cleaning up spills efficiently. But have you ever wondered how these absorbents are made and tested?
In this article, we’ll take a closer look at the production process and testing methods of oil absorbent pads, booms, and other cleanup products. Whether you work in the petroleum, chemical, or spill response industry, this guide will help you understand what makes a high-quality oil absorbent.
What Are Oil Absorbent Materials?
Oil absorbent materials are specially designed to soak up oil while repelling water. This makes them crucial for spill response in industrial sites, warehouses, marine environments, and chemical plants. These materials help prevent environmental damage, workplace hazards, and costly cleanups.
Types of Oil Absorbent Materials
Different absorbents serve different purposes. Choosing the right type depends on the type of spill, the environment, and the level of cleanup required.
1. Polypropylene Absorbents (Synthetic Absorbents)
This is the most common type, made from synthetic fibers. These are lightweight, durable, and highly absorbent.
- Common uses: Oil spills on water surfaces and industrial floors
- Examples: Oil absorbent pads, rolls, booms, socks
- Why Use Them?
- Made from melt-blown polypropylene fibers, these are the most common oil absorbents.
- Highly effective at absorbing oil-based liquids like petroleum, diesel, and hydraulic fluids.
- Hydrophobic (repels water), making them perfect for marine spills and rain-exposed spills.
- Durable and reusable in some cases, reducing waste.
Polypropylene absorbents are the best choice for high-efficiency spill control in industrial and marine settings.
2. Natural Fiber Absorbents
Natural fiber absorbents are made from organic materials like cotton, wool, coconut husk, or peat moss. These are eco-friendly alternatives.
- Common uses: Eco-friendly spill response in warehouses, factories, and outdoor sites
- Examples: Cotton mats, wool pads, coconut husk booms, peat moss absorbents
- Why Use Them?
- Made from renewable plant-based or animal fibers.
- Highly absorbent and biodegradable, making them a sustainable option.
- Some options, like cotton and wool absorbents, can be reused after drying.
- Peat moss absorbents can absorb up to 10 times their weight in oil and work well in outdoor spills on soil or gravel.
- Coconut husk booms are effective in harbors and shorelines as they float and contain oil slicks.
Great for businesses looking for a greener, sustainable spill management solution.
3. Biodegradable Absorbents
These products are designed to break down naturally, reducing environmental impact. These are becoming more popular in sustainable spill management.
- Common uses: Eco-conscious businesses handling minor to moderate oil spills
- Examples: Recycled cellulose pads, straw-based absorbents, corncob granules
- Why Use Them?
- Designed to break down naturally over time, reducing environmental impact.
- Straw-based absorbents are useful for land-based spills in farming, agriculture, and rural industries.
- Recycled cellulose pads offer good absorbency while being compostable after use.
- Corncob granules can be spread over workshop and warehouse floors to soak up oil before sweeping away.
They are ideal for companies prioritizing environmental responsibility while managing oil spills.
Key Takeaway:
The right oil absorbent depends on the spill type and location.
- For industrial and marine spills: Polypropylene absorbents are the best choice.
- For sustainable solutions: Natural fiber and biodegradable absorbents are great alternatives.
- For land-based spills: Peat moss, corncob, and straw absorbents work effectively.
Choosing the right absorbent ensures a faster, safer, and more effective cleanup process while minimizing environmental impact.
How Are Oil Absorbent Materials Manufactured?
Creating oil absorbent materials requires a carefully controlled process to ensure they are effective in spill response. From selecting the right materials to shaping and testing the final product, every step plays a role in making high-quality absorbents.
Step 1: Selecting Raw Materials
The first step is choosing the right material based on performance, durability, and environmental impact.
Polypropylene is the most widely used synthetic material. It is lightweight, highly absorbent, and resistant to chemicals. This makes it ideal for industrial and marine spill cleanups.
For eco-friendly options, manufacturers use natural fibers like cotton, wool, peat moss, or coconut husk. These materials offer strong absorption and are biodegradable, making them a good choice for land-based spills and sustainable spill management.
Some absorbents are made from recycled materials, helping reduce waste while still offering good oil absorption. These are commonly used in eco-conscious industries looking to minimize their environmental footprint.
Step 2: Processing and Fabrication
Once the raw materials are selected, they go through a processing stage to turn them into effective absorbents.
For polypropylene absorbents, the plastic is melted down and blown into fine fibers using a process called melt-blowing. These fibers are layered and bonded to create strong, oil-absorbent sheets.
For natural fiber absorbents, materials like peat moss or coconut husk are cleaned, treated, and compressed into pads, rolls, or loose-fill absorbents. Some natural fibers are woven into socks and booms for oil containment in water or on land.
Step 3: Shaping and Cutting
After processing, the absorbent material is shaped and cut into different forms based on how they will be used.
Absorbent pads and rolls are flat and flexible, making them perfect for wiping down surfaces or soaking up small spills in workshops and factories.
Booms and socks are long, tube-shaped absorbents used to contain spills on water or prevent oil from spreading on land.
Loose-fill absorbents, like granules or shredded fibers, are scattered over large spill areas to quickly soak up oil before being swept away.
Each form serves a unique purpose, ensuring spill cleanup is fast and efficient.
Step 4: Adding Final Enhancements
To make the absorbents even more effective, manufacturers apply special treatments.
A hydrophobic coating is often added to synthetic absorbents, making them repel water while absorbing oil. This is crucial for marine spills, where absorbents need to float and collect oil without becoming waterlogged.
Some absorbents are reinforced with extra layers for increased strength, preventing them from tearing or falling apart during heavy-duty use. This is important for industrial sites where absorbents need to withstand rough handling.
Every oil absorbent material goes through a detailed manufacturing process to ensure it is strong, effective, and suited for specific spill cleanup needs. Whether synthetic or natural, each absorbent is designed to help businesses respond to spills quickly and efficiently, protecting both the workplace and the environment.
How Are Oil Absorbent Materials Tested?
Before oil absorbent materials are sold, they go through strict testing to ensure they perform well in real spill situations. These tests check how much oil they can absorb, how well they retain it, and how durable they are.
Absorption Capacity Testing
This test measures how much oil the absorbent can soak up before it reaches full saturation. The goal is to ensure that absorbents can hold large amounts of oil without dripping or leaking.
High-quality absorbents should be able to absorb several times their weight in oil, making them efficient for both small spills and large-scale cleanups.
Retention Testing
Absorbing oil is one thing, but keeping it in is just as important. Retention testing checks whether the absorbent can hold onto the oil even under pressure.
If oil leaks out too easily, the absorbent is not reliable for industrial spill cleanups, transport, or disposal. Strong retention is crucial for preventing secondary contamination.
Hydrophobicity Testing
This test ensures that the absorbent material only soaks up oil and repels water. This is especially important for cleaning up oil spills in lakes, oceans, and rainy environments.
If an absorbent takes in both water and oil, it will become heavy and less effective. High-quality absorbents should float on water and quickly attract and trap only oil-based liquids.
Durability and Strength Testing
Absorbents must withstand rough handling, movement, and heavy oil loads. This test measures their tear resistance and stretchability to ensure they don’t fall apart during use.
For example, booms used in marine spills need to stay intact while floating in rough waters. Absorbent pads used in factories should not rip easily when soaked with oil.
A strong, durable absorbent means less waste, lower costs, and more effective spill control.
Environmental Safety Testing
For biodegradable absorbents, manufacturers check whether they break down naturally without harming the environment. This ensures that when disposed of, they don’t release toxic chemicals or microplastics.
Sustainable absorbents should decompose within months, leaving no long-term waste behind. This is important for companies looking to reduce their environmental footprint while managing spills.
Oil absorbent materials must pass multiple tests to ensure they are effective, durable, and safe for use. High-quality absorbents can hold large amounts of oil, prevent leaks, withstand tough conditions, and minimize environmental impact.
Choosing well-tested absorbents means faster cleanup, fewer risks, and a safer workplace.
Why Quality Manufacturing and Testing Matter
Using high-quality oil absorbent materials is just as important as cleaning up a spill quickly. Poorly made absorbents can fail, leak oil back into the environment, or create additional hazards. That’s why choosing well-manufactured and tested absorbents is critical for safety and efficiency.
A low-quality absorbent may look effective at first, but if it can’t hold oil properly, it can cause more harm than good. Imagine cleaning up an oil spill, only for the absorbent to start leaking oil back onto the ground or into the water. This leads to secondary contamination, making cleanup harder and more expensive.
Investing in high-quality absorbents can also save time and money. Superior materials absorb more oil, work faster, and require fewer replacements, cutting down on waste and overall cleanup costs.
Additionally, many industries must follow strict environmental laws regarding spill management. Using certified absorbents ensures compliance with safety and environmental regulations, helping businesses avoid fines and legal issues.
Final Tip:
Always choose lab-tested and certified absorbents from trusted suppliers. This guarantees better performance, improved safety, and long-term cost savings.
Choosing the Right Oil Absorbent Materials
Selecting the right oil absorbent material depends on the type of spill, where it occurs, and the best material for the job. Using the wrong absorbent can slow down cleanup, increase costs, and even make spills worse.
1. Consider the Type of Spill
Different oils and chemicals require different absorbents.
- Light oils (gasoline, diesel, lubricants) need absorbents that work quickly and hold large amounts of liquid.
- Heavy crude oils require stronger, high-capacity absorbents that won’t tear or break under pressure.
- Chemical spills may need specialized absorbents designed to handle toxic or reactive substances safely.
2. Think About the Cleanup Environment
The location of the spill affects which absorbents will work best.
- For spills on land (factories, workshops, warehouses), absorbent pads and rolls are effective for wiping surfaces and soaking up pooled oil.
- For spills on water (oceans, lakes, harbors), booms and floating pads are ideal because they absorb oil while repelling water.
- For outdoor spills on soil or gravel, loose-fill absorbents like peat moss or corncob granules can quickly absorb oil without harming the ground.
3. Choose the Right Material
- Synthetic absorbents (polypropylene) are best for fast, high-volume oil absorption in industrial settings and water-based spills.
- Natural fiber absorbents like cotton, wool, and coconut husk are great for eco-friendly spill control in land-based spills.
- Biodegradable absorbents break down naturally, making them ideal for sustainable spill management.
Conclusion
Oil absorbent materials are essential tools for managing spills in industrial and environmental settings. Their manufacturing process involves careful material selection, advanced processing techniques, and strict quality control. Testing ensures they perform well in real-world spill situations.
By understanding how these materials are made and tested, businesses can make better purchasing decisions and improve their spill response efficiency.
For top-quality, lab-tested oil absorbent pads, booms, and spill control products, trust Big Nano Technology (BIGNANOTECH). Contact us today to find the right solution for your industry!